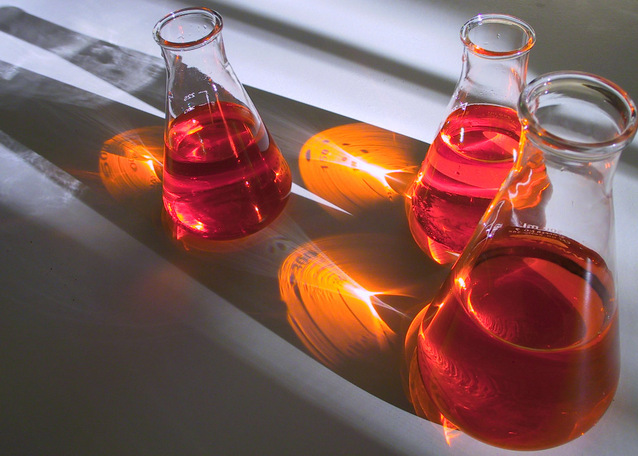
Facilities that embrace the Industrial Internet of Things, or IIoT, will remain competitive while those that don’t will be left behind. VEGA has already begun making strides to embrace Industry 4.0.
The food and beverage industry is more competitive than ever. A global market and consumers’ ever-changing tastes leave no room for error, so plants need to be able to act quickly and adjust to maintain profit margins. Facilities that embrace the Industrial Internet of Things, or IIoT, will remain competitive while those that don’t will be left behind.
In order to fully embrace Industry 4.0, facilities have a number of needs that must be met. They’ll need more types of reliable and accurate data, a system to analyze the data, and finally, a way to act on that analysis. At first glance, each of these needs may appear to be big obstacles to overcome, but upon further inspection, these are simply opportunities for continuous improvement.
Acquiring all of this data is a big endeavor, but it’s made easier with new and advanced sensor technologies. Smart pressure sensors, point level switches, and radar level sensors already help plants automate processes, improve efficiency, and save energy. Bringing all the sensor process data together using the IIoT will help drive smarter and faster complex business decisions, which will only help to make further improvements to efficiency and energy conservation.
VEGA has already begun making strides to embrace Industry 4.0. VEGA sensors come equipped with digital communication protocols for easier transmission of information to the cloud. The measured value and event memory built into every VEGA instrument allows continuous tracking of changes in the sensor and in the process. VEGA instruments are continually monitoring the most important measurement parameters. All this data can be read and analyzed with a PC using DTM or EDD if service is ever required.
Detailed, on-demand diagnostic function tests, as well as continuous diagnostics, ensure the sensor is always functioning properly and informs and documents the status of the sensor for the user. VEGA instruments are equipped with a variety of asset management functions for preventative maintenance. Standardized status messages according to NAMUR NE 107 are displayed in plain text as well as in the form of graphical symbols and transmitted digitally.
Plus, VEGA sensors can be accessed wirelessly using a secure Bluetooth connection. All these features are a part of the steady march toward one inevitable goal – an interconnected plant better managed from start to finish.
New, intelligent sensors increase economies of scale in production, enabling operations to maximize the available space in vessels of all shapes and sizes, thereby increasing throughput and revenue. These same sensors provide key data points, which help to maximize plant availability.
Imagine during peak production times an unexpected shutdown occurs. This can be a very expensive loss of production and revenue generation. This is where digital diagnostic information becomes invaluable.
Most sensors show signs of wear and tear slowly at first, and then all at once. With self-diagnostic tools built into the sensor, error messages are sent directly over the digital highway to operators who can provide preventative maintenance or if necessary, a replacement. Both options reduce the number of unplanned shutdowns due to sensor failure.
Driving a sensor to failure is costly, and catching errors before a sensor fails altogether saves money and time. Plus, having access to digital diagnostic information can and often does minimize governmental, quality and safety compliance violations by giving operators insight into measurement deviations at an early stage before it becomes a critical failure or event.
As every sensor outputs vital data and information, it all funnels into one place – the cloud. All of this data is constantly being crunched and analyzed to help everyone from the plant floor to the board room make more informed decisions more quickly, and this provides a number of benefits.
For starters, the data can be used to secure the supply chain and maximize the logistics of feedstocks to make products. The VEGA Inventory System does just that for a number of industries by monitoring inventories and automatically notifying suppliers and their logistics operations when a new order or delivery needs to be made. Plants no longer worry about running out, and suppliers aren’t wasting time waiting for a silo or vessel to be emptied before unloading their delivery.
The same principles can be applied throughout the plant to maximize inventory efficiencies. Real-time information keeps people on the plant floor informed of the entire manufacturing process, which helps reduce losses due to lost product and keeps the overall process running smoothly.
When it comes to planning for the future and making necessary changes, IIoT can help with the transition. Whether these are small changes to simply increase quality or major changes affecting an entire production line, planning and implementing changes becomes easier using the data obtained from a connected plant.
Industry 4.0 and IIoT are no longer buzz words – it’s the present. Successfully executing these changes may seem overwhelming at first, but instrumentation companies like VEGA have been preparing for the next inevitable, evolutionary step in manufacturing, and we’re here to help guide our customers.
Businesses cannot control or act on that which they don’t measure. Using smart sensors wisely will help users get a step ahead of the competition to gain market share and grow their business for years to come. Because in the future, the companies who can move quickly according to market changes while minimizing waste and energy usage will be the companies who succeed.
Source: Food Processing